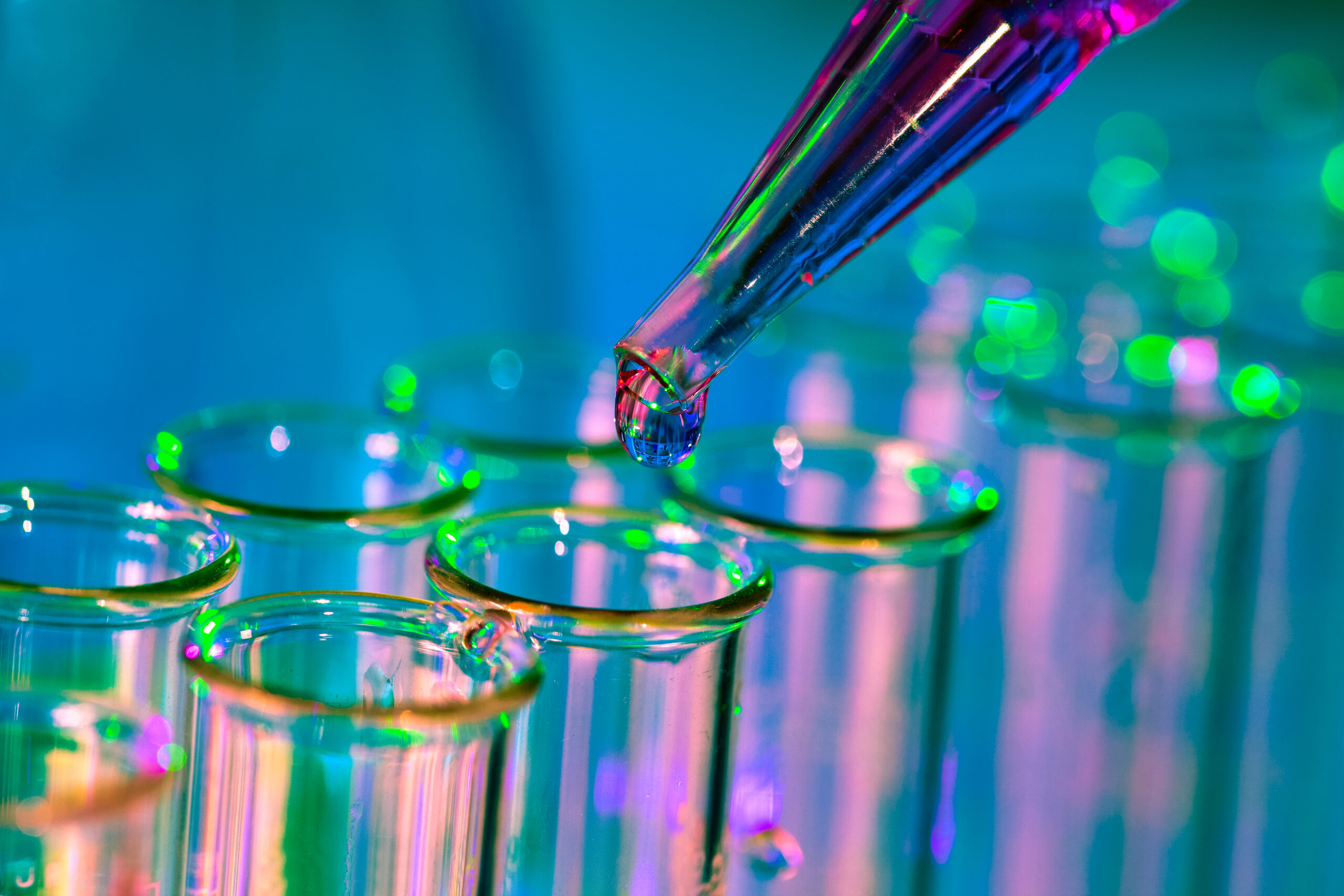
Scientific Design Maximizes Improvements with LEAN/5S
by
Michael Womack
BACKGROUND
Scientific Design (SD) was founded 76 years ago by chemical entrepreneurs looking to compete with large international chemical corporations. This Little Ferry, New Jersey company’s success has been a result of their entrepreneurial spirit as a driving force for how they operate today. They have become a global leader in the development, licensing, and catalyst supply of proprietary processes for the production of Ethylene Oxide (EO), Ethylene Glycol (EO/EG), Bio-Ethylene, Bio-EO, Bio-EG, EO derivatives, Polyols, and Maleic Anhydride.
To maintain their position as industry leaders, they had to overcome challenges that impacted their growth.
CHALLENGE
Efficiency is one of the biggest concerns for manufacturers looking to cut down on wasted time and resources. Companies who can maximize the workload by streamlining work processes will decrease stress for their employees while increasing productivity. Driven by several factors, including a philosophy of continuous improvement, corporate value of being a “great place to work,” principles of workplace standardization and organization dovetails, and the desire to improve employee engagement and value, Scientific Design’s leadership saw many areas for growth. To be successful, companies must look at areas where they can make changes. Scientific Design’s leadership is a perfect example of this. Their team expressed a need to improve their research & development and production processes and strategies to better support their workforce.
Scientific Design’s leadership identified LEAN/5S as necessary to improve workplace efficiency. NJMEP’s expert LEAN specialists to consult with clients like SD as well as host courses such as Overview of Lean Operations and Principles of Lean Manufacturing to upskill workforces. Scientific Design’s leadership needed a LEAN/5S expert, teacher, and coach to achieve their goal to establish a strong transformational, internal LEAN/5S team. After several discussions with their NJMEP Account Manager, they were introduced to a team of experts who have the experience and personality to match their corporate culture and understood what was needed to implement LEAN/S5.
SOLUTION
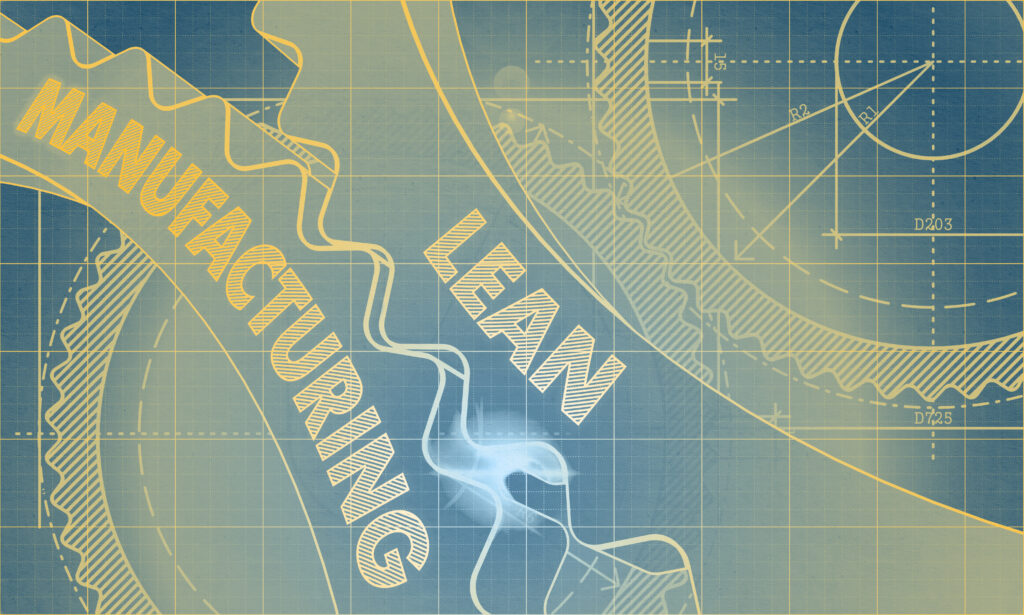
NJMEP created a strategy, and consistently engaged with Scientific Design’s team to ensure LEAN/S5 strategies and methodologies were properly implemented throughout the process. NJMEP worked to establish a healthy relationship between both organizations while ensuring the program was effective and reaching the goals outlined for the project through regular contact. Additionally, NJMEP’s Account Manager regularly participated in the management report session at the end of each event, building trust and communication that exceeded SD’s expectations and ensured the project achieved the client-expected results.
RESULTS
Scientific Design’s leadership was pleased with NJMEP’s solution to implement LEAN/S5. There was a noticeable boost in efficiency and employee morale due to the LEAN/5S events. SD employees are no longer wasting time searching for tools or walking from one side of the building to another to conduct required tests since the equipment has been relocated to the appropriate lab. In turn, these efficiencies have resulted in significant savings of time and money to reinvest into their business.
Another notable difference is a workplace culture that encourages self-direction and self-discipline where employees take pride in their workspaces. As a result, the staff is more respectful when using spaces that aren’t their own. They’re now looking forward to next step improvements that to be rolled out across the company, in addition to those implemented at their plants and labs.
“Seeking guidance from NJMEP has been instrumental in identifying the areas LEAN/5S could improve. This partnership has not only turned their company around, it has also given them the blueprint for success. They are recommending businesses enlist NJMEP’s services,” explained Claudine M. D’Angelo, Scientific Design Marketing & Communication Specialist.
The impact listed below are the quantifiable impact of working with NJMEP over the past 12 months:
- Jobs Created: 1
- Jobs Retained: 5
- Cost Savings: 500,000