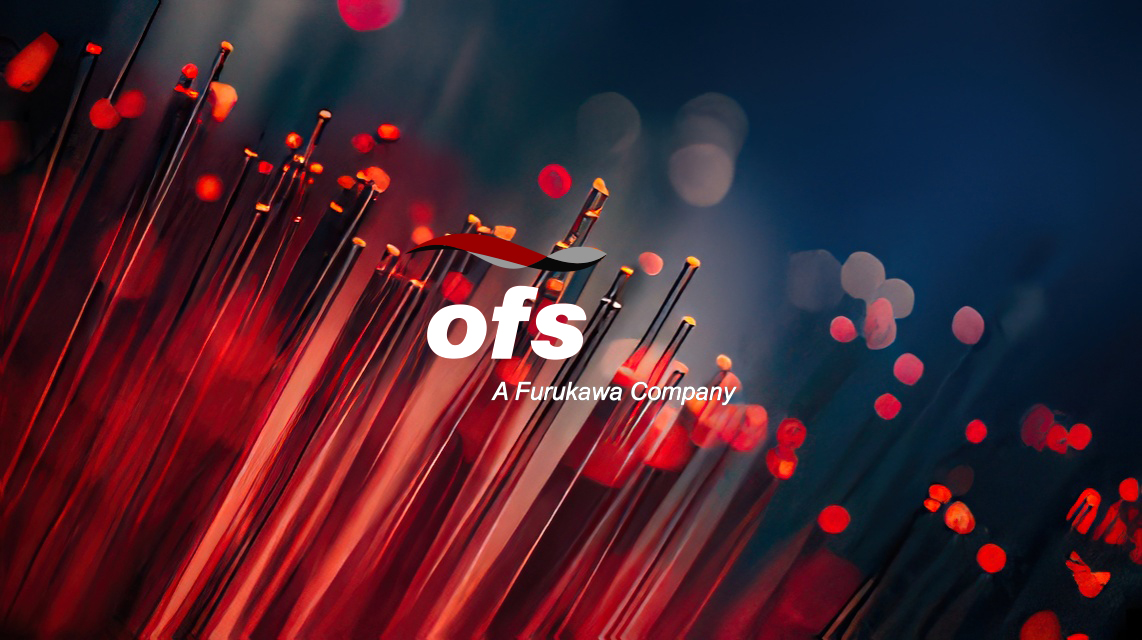
HIGH-LEVEL LEAN TRAINING AT OFS CHANGES EMPLOYEE MINDSETS TO THINK LEAN
by
NJMEP
Background
OFS is a leading provider of innovative optical fiber solutions, focusing on the design, manufacturing, and delivery of fiber optic products. With a rich history rooted in Bell Labs’ pioneering work, OFS offers cutting-edge solutions for telecommunications, medical, industrial, and defense applications. The company emphasizes quality, performance, and sustainability, leveraging advanced technologies to meet diverse customer needs worldwide. By maintaining a commitment to excellence and continuous improvement, OFS aims to drive progress in optical communications and beyond.
Challenge
Cari August, Manufacturing Manager for OFS, said the idea behind refreshing LEAN training arose from a need for a refresher following the COVID-19 pandemic, where she says she felt like a new employee even though she’d been working at OFS for over two years. She wanted to refresh not only the production teams, but also management personnel so that all employee mindsets were aligned and thinking LEAN. On top of that, the company was experiencing a rapid uptick in production volumes.
“We had a particular production area where the volumes were higher than we expected sooner than we expected,” says August, “So we were looking to address some capacity constraints.”
August, along with her Production Manager Maria Fernandez and HR Manager Molly Griffith, set out to work with their NJMEP Account Manager to find ways where they could have the biggest impact on aligning their production and management teams, while also addressing their new capacity constraints. Having completed successful LEAN training in the past, it was decided that a high-level LEAN overview is exactly what OFS needed to tackle its challenges.
Solution
NJMEP’s expert resource provided a high-level review of LEAN Enterprise Principles through consultation, facilitation, and training. The project aimed to reinforce LEAN concepts among OFS supervisors and engineers via onsite sessions involving teaching and hands-on application. The proposal included a LEAN overview and a targeted Plan-Do-Check-Act (PDCA) event—an iterative process integral to LEAN management, focusing on continuous improvement of products, people, and services through planning, executing, checking results, and implementing process improvements. The project was estimated to require 10 hours of work. The high-level LEAN overview project was conducted in two sessions over two days onsite at OFS, combining teaching and hands-on application. Sessions were scheduled at mutually convenient times, minimizing operational impact. A single point-of-contact at OFS coordinated efforts, and key personnel were involved as needed.
NJMEP’s resource prepared and conducted two one-day sessions to implement process improvements. Day one included a LEAN overview with a high-level review of major LEAN tools and methods through lectures and discussions. Targeted operations for PDCA demonstrations were identified. The implementation phase included a targeted PDCA event to apply proposed improvements, providing hands-on training and reinforcing the overview training. The goal was for OFS staff to understand the need for these improvements and how they would enhance company operations, making work more enjoyable and fulfilling by eliminating chaos and waste.
Results
One of the most notable results from the recent High-Level LEAN Overview project is a change in the mentality and behavior of technicians, says Maria Fernandez, Production Supervisor. “What I see and I like best is that [the project] has also promoted teamwork,” adds Fernandez.
As with most LEAN training, the work doesn’t stop at the end of a successful LEAN project. LEAN thinking is all about continuous improvement, and that’s something Cari August and the OFS team have certainly taken to heart.
The following results were cited as a direct result of engaging with NJMEP 12-18 months following the conclusion of the project outlined above.
- New Sales: $200,000
- Jobs Retained: 2
- Cost Savings: $50,000
Molly Griffith, HR Manager at OFS, says that engaging with NJMEP has helped take some of the burden off the shoulders of a small company like OFS. “With NJMEP being as proactive as they are with reaching out and creating connections for us and offering services, it’s just taken a lot of that admin work out of trying to find resources manually on our own.”
“NJMEP’s support has helped us to engage with New Jersey employee upskill grant opportunities that would otherwise be too cumbersome for us to take advantage of,” says August. “I would definitely recommend companies investigate NJMEP and what they can offer.”
Cari August, Manufacturing Manager for OFS