Unionwear Maintains a Competitive Edge
American Textile Manufacturer Thrives in New Jersey
Unionwear, an American apparel manufacturer based in New Jersey, celebrates the company’s effort to implement lean manufacturing. Founded in 1992, today they employ 175 people. Mitch Cahn, president, and CEO uses his business as an example of why New Jersey is an ideal place to manufacture.
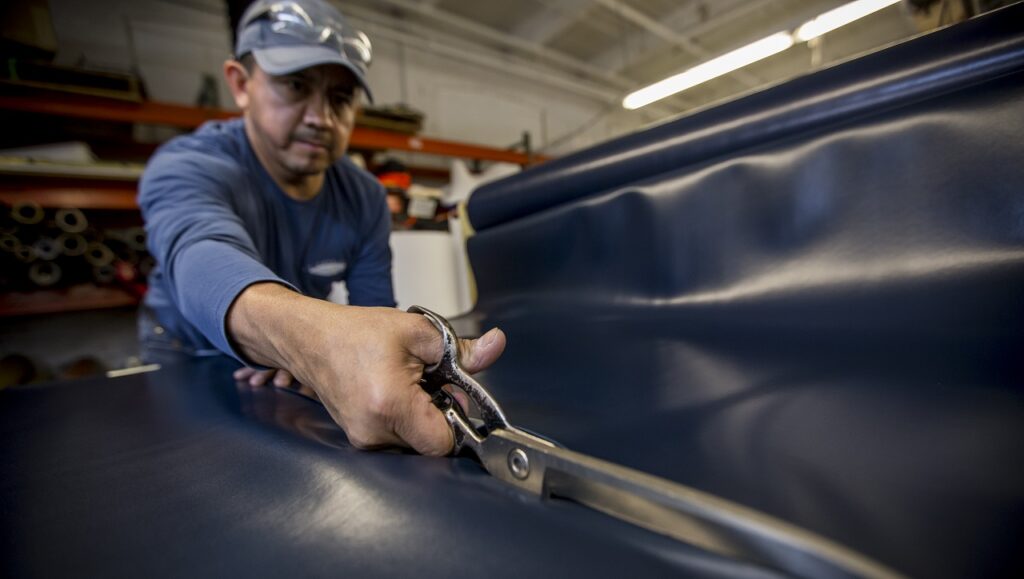
One reason Unionwear can remain incredibly competitive in New Jersey is its willingness to integrate best practices in order to create an efficient and productive manufacturing environment. Lean manufacturing is a strategy aimed at eliminating waste from production by applying processes and procedures that have a dramatic impact on the efficiency, effectiveness, and profitability of the company. Lean manufacturing utilizes many “common sense” strategies that might at first sound easy to put into action. However, creating a truly lean manufacturing operation can present challenges, and these processes and procedures are often difficult to maintain over time. There is a clear distinction between understanding the concepts of lean and implementing it on the shop floor.
How Unionwear Conquered Lean Manufacturing
“We had been struggling to implement lean manufacturing constantly for the last 12 years and it’s a struggle because lean flies in the face of human nature,” said Cahn. “The key principles to wrap your head around are reducing waste. Before we started lean manufacturing [employees] were spending 30 minutes working for every hat produced. They are now sending five minutes to produce a hat.”
Lean manufacturing is centered around the idea of creating more efficient processes, working smarter not harder, and eliminating waste in all its forms. Cohn identified that employees were spending too much time searching for fabrics. If Unionwear was able to reduce the time it took to find the correct materials for one employee by 5 seconds, and that employee repeats that process 10 times a day, that could equate to just about three and a half extra hours that one employee can spend on production per year. Scale that up to an entire facility employing 175 individuals and the ROI is undeniable.
Unionwear began to focus on “Made in USA” branding, as well. This proved to be a major selling point for American companies and Cahn was confident people were willing to pay a premium for ‘Made in USA’ products. He stated, “We do not have to be as inexpensive as goods made in China. We just need to be in the ballpark,” They are able to maintain a competitive price point due to their implementation of lean as well as through a comprehensive grasp of proper supply chain management and computer automation.
“We want stuff coming right of the truck and going into a product and then we want that product coming right off the production line and being shipped to a customer,” he stated. “That reduces our expenses of keeping inventory and storing inventory.”
Cahn sits on the board of directors for NJMEP, a chairman of the Newark Workforce Development Board and a director of the Newark Regional Business Partnership. He is a champion of New Jersey manufacturing and insists the state offers an incredible environment for manufacturing because of its workforce, access to ports, and its manufacturing infrastructure.
His impression of New Jersey manufacturing comes from years of experience in the sector and state. Cahn’s success is a testament to his leadership, the ability to implement lean, and brand his products as “Made in USA”.
Unionwear worked with NJMEP to develop a comprehensive lean manufacturing plan and to put it into practice. NJMEP’s lean manufacturing services are designed to make implementing this proven and effective business strategy manageable for a business of any size. For more information on lean manufacturing services, contact NJMEP and begin taking advantage of all the resources, support and experience available.
The story first published in Manufacturing Matters! Sign up and receive the NJMEP’s quarterly magazine.