The Power of LEAN Facility Layouts: Driving Efficiency and Excellence in Manufacturing
In the dynamic manufacturing landscape, the evolution of LEAN thinking is at the forefront. While the industry has been abuzz with the term Industry 4.0, the transformative impact of LEAN methodologies when reviewing facility layouts cannot be overlooked. LEAN experts consistently witness significant and enduring improvements in manufacturing facility efficiency through optimized layouts. A few simple changes or approaching a project with a unique perspective can dramatically improve the productivity of an operation.
Common Challenges in Manufacturing Facility Management
Manufacturing facility managers today often grapple with familiar challenges such as the following:
- Operating at full capacity with production bottlenecks
- Long production and lead times
- An undesirable work environment
Whether you’re new to LEAN principles or exploring opportunities for improvement, this article will assist you with understanding what a LEAN facility layout is and how it can help resolve some of your biggest challenges.
What is a LEAN Facility Layout?
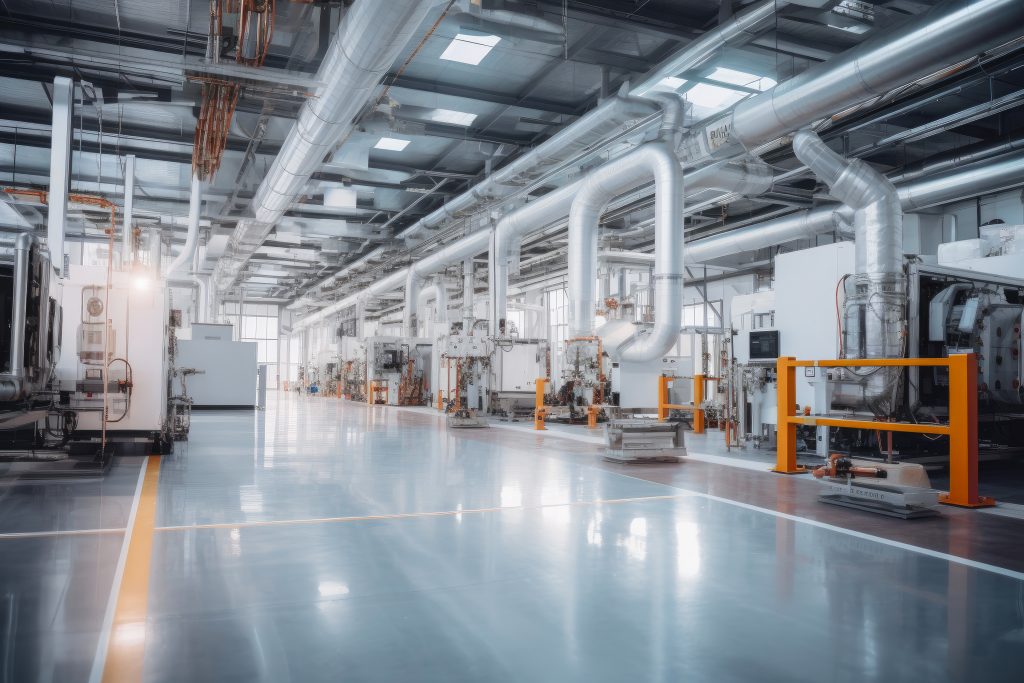
An effective manufacturing facility layout is pivotal to successfully managing production. It not only impacts operational efficiency but also influences overall company operations, including production processes, inventory management, dispatch, and administration. An effective facility layout varies based on your desired outcomes. We define an effective facility layout as one that embraces LEAN principles to create an optimized environment. LEAN methodologies focus on waste elimination, delivering value to customers with reduced costs, improved quality, shorter lead times, and increased safety and morale.
LEAN facilities prioritize seamless material and information flow, minimizing handling time and floor space, shortening lead times, boosting productivity, and enhancing quality. Whether you’re designing new operations or revamping existing ones, a LEAN facility layout offers flexibility and efficiency in space utilization.
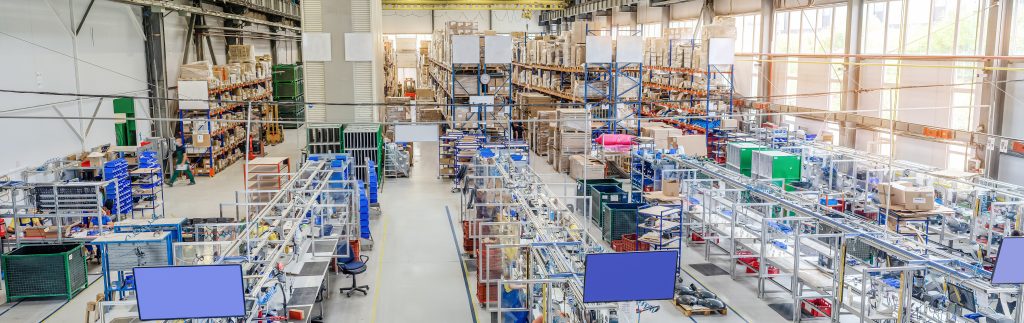
Differences Between Traditional and LEAN Facility Layouts
There are several key factors that distinguish a LEAN facility layout from a traditional one:
Process-Based versus Value Stream-Focused
Traditional facility layouts center around process-based departments, with similar machines grouped into functional work centers or workshops. This setup often leads to high work-in-process inventory and extended lead times. In contrast, LEAN facility layouts prioritize value streams, connecting processes horizontally to minimize material handling and streamline operations.
Cost-Per-Unit versus Flexibility
Traditional mass production relies on large equipment for cost-effective batch production. While these machines may be efficient on a per-unit basis, they impede material flow and are less adaptable to changing demands. Lean layouts opt for smaller, flexible equipment tailored to specific product families, enabling quick changeovers and smaller batch sizes.
Appearance versus Functionality
Traditional facility layouts may prioritize aesthetics over functionality, leading to excessive space between machines and work areas. This can result in increased work-in-process inventory and inefficient material flow. In contrast, LEAN facility layouts focus on functionality, minimizing space between machines to prevent inventory buildup and enhance overall flow.
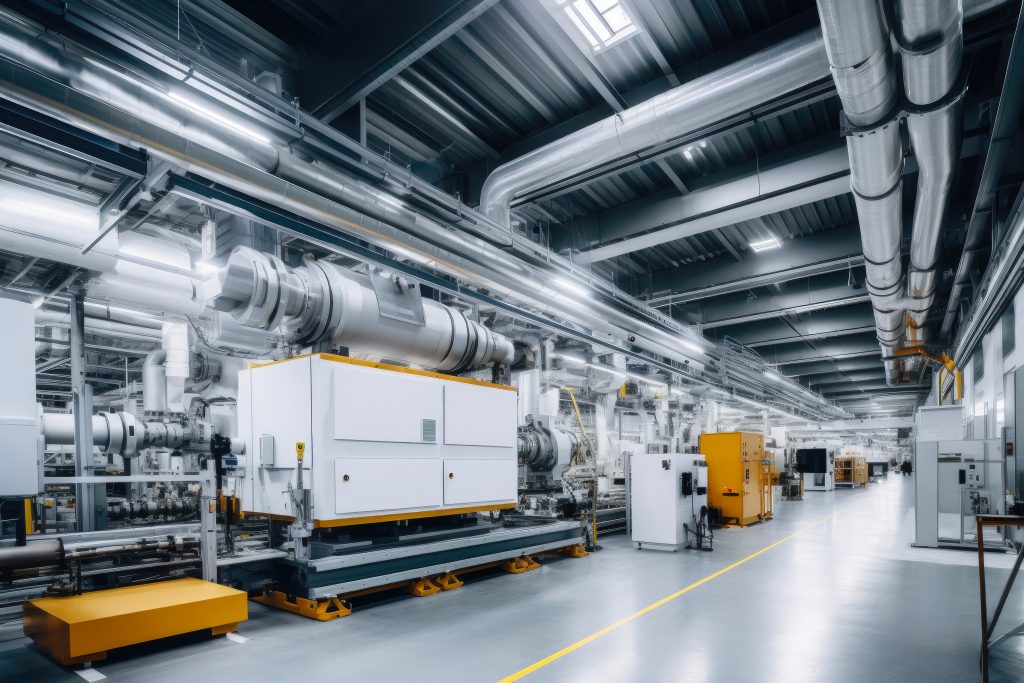
Characteristics of an Effective LEAN Facility Layout
Determining whether your manufacturing facility embodies LEAN principles involves assessing specific criteria that align with LEAN methodologies. First, consider the connection to customers: LEAN layouts prioritize customer-centric value streams, aiming for quick response times and defect-free products by aligning processes with customer demand to drive continuous improvement and satisfaction. Secondly, evaluate flow: a LEAN facility layout emphasizes continuous flow throughout all processes to minimize waste and ensure efficient material, information, and people flow, promptly identifying and removing any blocked flows. Next, focus on waste reduction: LEAN layouts target waste reduction across various forms, optimizing production with smaller batch sizes, reduced inventory, and streamlined processes. Additionally, assess flexibility: an effective LEAN layout is adaptable to changing demands, production methods, or equipment, accommodating future expansions and new product launches to maintain long-term operational agility. Lastly, consider the establishment of a new standard: LEAN facility layouts set a benchmark for operational excellence, promoting collaboration among stakeholders and fostering a culture of continuous improvement throughout the facility. By evaluating these criteria, you can assess the degree to which LEAN principles are integrated into your manufacturing facility layout.
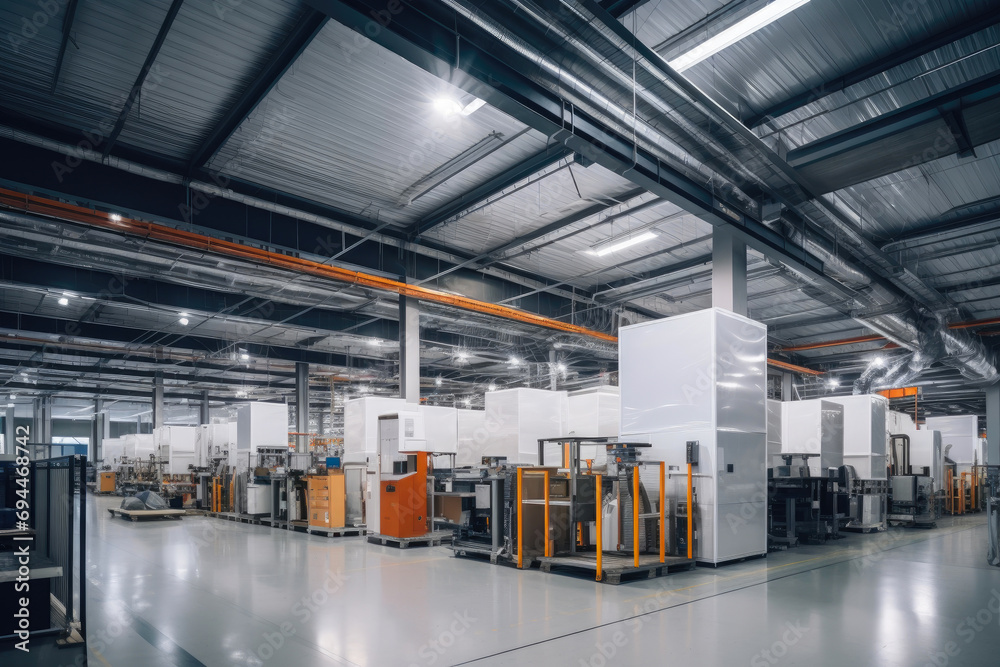
The Benefits of LEAN Facility Layouts
Implementing a LEAN facility layout may involve initial challenges, but the benefits far outweigh the efforts:
- Minimized material handling and floor space use
- Enhanced product quality and reduced defects
- Lower work-in-process inventory and shortened lead times
- Streamlined workflows and increased visibility of waste
- Cost savings and improved production efficiency
- Enhanced workforce safety, morale, and engagement
- Flexibility to accommodate future changes and expansions
A LEAN facility layout is a journey of continuous improvement, with room for refinement and enhancement. Embrace LEAN principles to drive efficiency, excellence, and competitiveness in your manufacturing operations. At NJMEP, we’re committed to empowering businesses with the resources, tools, and insights needed to embark on this transformative journey towards operational excellence.