South Jersey Revitalization Summit Aims to Create New Talent Pipeline
If You Help Build It, The Workers Will Come
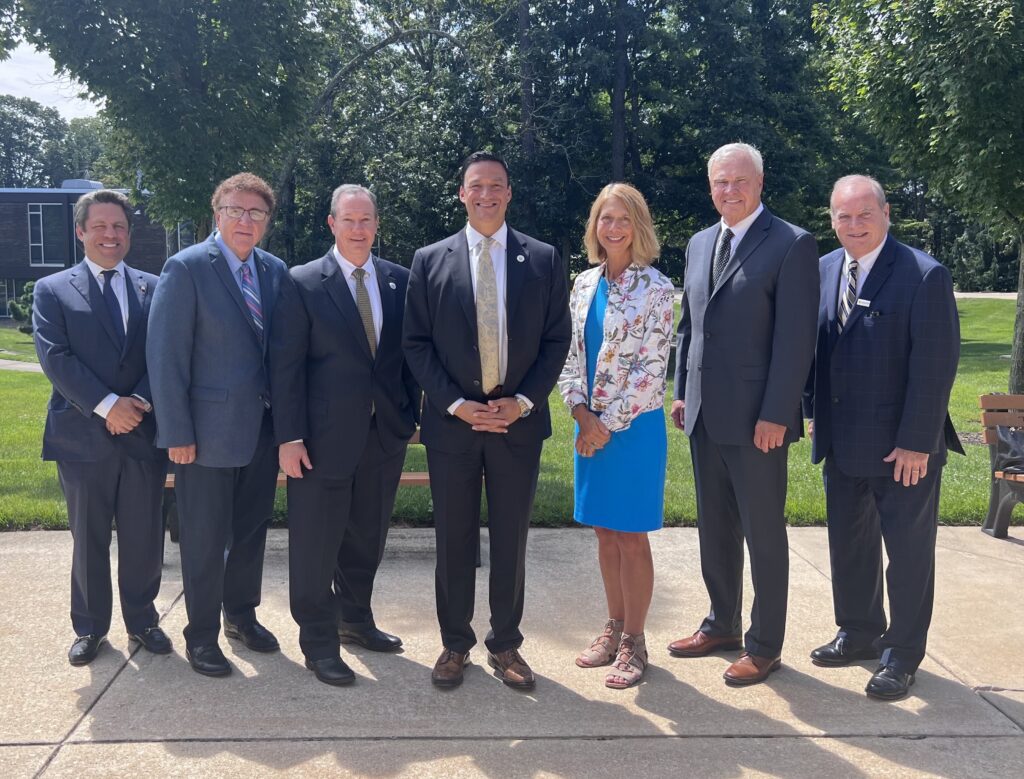
Bringing Together Industry, Academia, and State
In August, the New Jersey Manufacturing Extension Program (NJMEP) partnered with Rowan College of South Jersey (RCSJ), Community College of Morris (CCM), District 1 lawmakers, and South Jersey Industry Leaders to host the South Jersey Manufacturing Revitalization Summit at Rowan College of South Jersey. The event was part of ongoing efforts to revitalize underserved and disconnected areas of manufacturing in South Jersey. All those in attendance joined for a panel discussion on how State, Academic, and Industry partners can assist the more than 3,000 South Jersey Manufacturers with enhancing productivity, performance, and profits— and how these private-public partners can come together to help solve some of the industry’s most pressing challenges.
Addressing Labor Challenges
NJMEP CEO Peter Connolly sat down with Dr. Fred Keating, President of RCSJ, Dr. Tony Iacono, President of CCM, local business leaders, and Senator Michael Testa (NJ-D1) to discuss plans to build a 25,000-square-foot manufacturing technical training facility at RCSJ, as part of South Jersey Revitalization efforts. The goal of the Summit was to illustrate the eagerness of industry, government, and higher education to reinvest in South Jersey and to convince manufacturers to get involved in these revitalization efforts, or as Dr. Keating states—for manufacturers to have some ‘skin in the game.’ The plan is to create a new talent pipeline that will feed South Jersey Manufacturing’s critical need for skilled workers. This is a concept Dr. Iacono of CCM has experienced firsthand, having worked with local manufacturers and legislators in North Jersey on expanding Morris’s technical training capabilities—expanding the training facilities at CCM from 11,000 square feet to over 30,000 square feet, and creating new training programs and filling the facilities with advanced manufacturing equipment that was donated in part by local manufacturers. In North Jersey, manufacturers appear to be receiving the message loud and clear—that the pathway toward solving the skills gap and labor shortage is working with industry partners, academia, and government.
It’s no secret that with an aging workforce, the labor shortage is the top challenge for manufacturers in New Jersey and beyond. Peter Connolly, NJMEP CEO, adds that transportation, supply chain, and red tape are some of the biggest hurdles as well. “When you look at New Jersey, we have about 11,000 manufacturers, most of them located in the northern half, and the southern part of New Jersey is an underserved market,” says Connolly.
“We [NJMEP] are going to work and help refocus efforts on Southern New Jersey manufacturing and help connect the dots in terms of making this region more competitive, profitable, and accessible for businesses,” he adds. “And it starts with industry and academia coming together and facilitating the creation of a brand new talent pipeline, right here at Rowan College of South Jersey.”
Peter Connolly, CEO, NJMEP
Manufacturers Need To Get Involved
During the panel discussion, industry leaders and partners offered some insights into how manufacturers must pivot with the changing socioeconomic landscape to keep up with workforce demands. Ray Compari, City Administrator in Millville, offered his input on combating the skills gap and labor shortage in South Jersey. “Look at your talent pool as being vertically integrated,” says Compari, “What that means is you can’t wait for donut-makers to give you the donuts, you’ve got to be involved in the process early on.” He goes on to cite companies like Cisco, Caterpillar, Lockheed Martin, Motorolla, and Mercedes-Benz—companies he’s worked with in the past—and he says that these manufacturers have been looking at the workforce as a vertical integration for the past decade. They have summer internships, they’re involved in high schools and community colleges, they’re identifying high potential talent, and they’re building and investing in talent very early on—as he echoes Dr. Keating’s sentiment— these manufacturers have ‘skin in the game.’ His sentiments illustrate that manufacturers can’t keep asking for the laborers they need—they need to start investing in the workforce they want. Lauren Mufalli, Human Resources Director at South Jersey Glass & Door (SJG&D) and South Jersey Revitalization Summit panelist, says that their business has already tapped into this potential on a micro level and has seen the benefits. SJG&D, a 90-year-old glass and window manufacturer and installer based in Vineland, and one of the largest employers in the industry in South Jersey, has had to get creative to find a new talent stream and fill its ranks as it expands operations. One of the ways they’ve been able to combat the labor shortage was by partnering with academia.
“We partnered with Tech,” says Mufalli, “And we realized that even the amount of training these 16- or 17-year-olds had was monumental. We saw that they were even outpacing some of our current workforce,” she adds. “We’ve seen that [partnering with technical schools] works. The individuals that we’ve hired from Tech, they’re so excited to see what they’ve learned and actually apply it in a real-life setting— and then to get paid on top of it—they think they’ve won the lottery,” adds Mufalli enthusiastically, sending a pang of laughter through the audience.
The manufacturing sector has consistently struggled to appeal to younger generations of students and workers, and much of this failure is due to a lack of exposure—simply put, young people don’t realize that there are opportunities for a career in manufacturing. For Mufalli, it’s about empowering these young people and showing them that they’re part of something bigger. “They feel empowered, they feel self-worth, that gratification of really being successful and part of a team, that what they do matters, and that we need them to succeed,” she adds. “To continue that is imperative for us [as manufacturers] to be successful.”
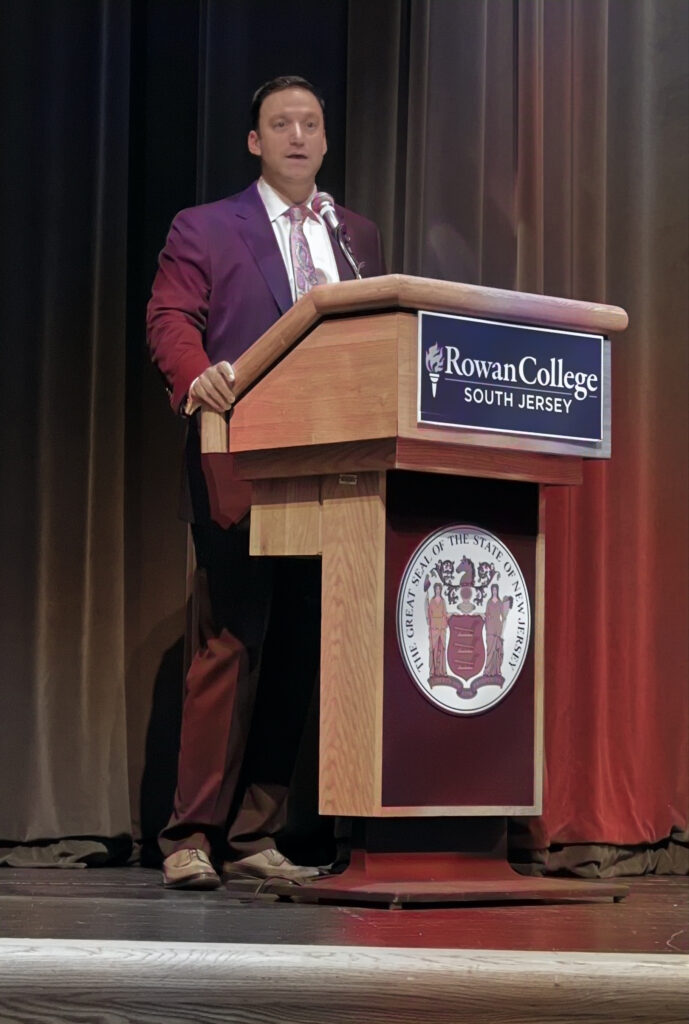
What’s Next For South Jersey?
For Senator Michael Testa, who’s been an ardent supporter of manufacturing, the next phase in the South Jersey Revitalization initiative is clear. “We need to have buy-in from local manufacturers to have ‘skin in the game,’ to support what is happening at Rowan College of South Jersey and at County College of Morris,” says Testa. The idea has been proposed to create a new talent pipeline that helps provide New Jersey’s youth with alternatives to the traditional four-year degree program. CCM is already on the field, with their 30,000 square foot state-ofthe- art training facility in the north, and with support from local manufacturers in North Jersey. Now, it’s time for manufacturers in the south to get on board and help facilitate the creation of a new talent pipeline, with CCM being the North Pole for manufacturing training and RCSJ as the South Pole.
“We have our little piece of the puzzle right here in Cumberland,” says Dr. Keating, referring to RCSJ. “We have a visionary leader, we have people that want to do something, but today’s going to be an acid test. People are asking me, ‘What’s the next step?’—the next step is for me to go out and get the partners in the room and hopefully get the agreement that we’re all in this together, and manufacturers can’t be spectator,” he adds, “You’re going to have to be a participant.”
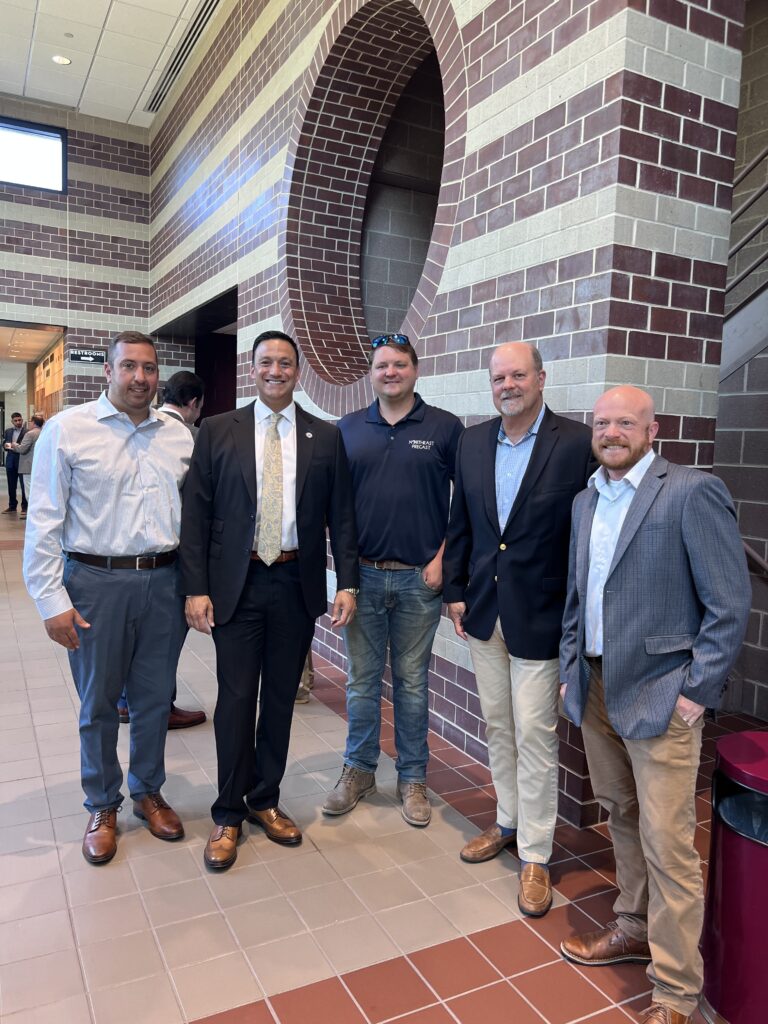
How Can South Jersey Manufacturers Get Involved?
Senator Michael Testa seconds Dr. Keating’s call to action: “It’s incumbent upon the Manufacturers to be involved, whether it’s with the Chamber of Commerce of South Jersey, NJBIA, and of course, with NJMEP—who’s been a monster partner for manufacturing,” says Testa.
Ray Compari, a Management Executive with ties to academic, corporate, and legislative consulting over the course of his career, says that manufacturers are in a unique position to contribute to the latest innovation in manufacturing—a new talent pipeline optimized for manufacturers, by manufacturers. “Tell us what your competencies are—what the knowledge, skills, and abilities are that are necessary to run your operations,” he pauses, gesturing at his fellow panelists Dr. Keating and Dr. Iacono, “And these guys will build a program to suit that.”
“One of [Dr. Iacono’s] discussions was partnerships . . . We need that, whether it’s legislative, government, academic, associations, or industry—we need to work this together.”
Peter Connolly, CEO, NJMEP