Manufacturers Meeting Increased Demand by Getting Lean
Reducing Waste, Improving Efficiently, Productivity, and Creating a Smoother Running Facility
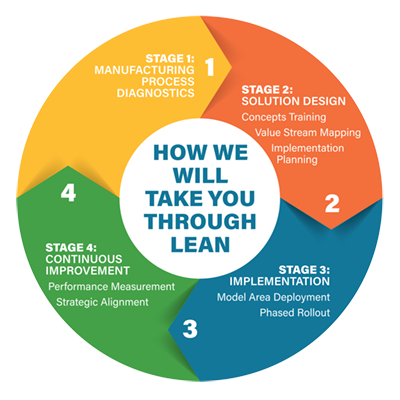
Lean is becoming a sought-after skill set for organizations seeking to fill open manufacturing positions. More employers are looking to hire a workforce that has had lean training, according to the recruiting firm, The Avery Point Group (APG). The trend is shifting from Six Sigma to Lean based on their findings from major internet job board postings that show the skills manufacturers are requesting from applicants. Manufacturers are focused on improving efficiency and eliminating waste, two areas where lean manufacturing excels.
Though Six Sigma still has value, lean is becoming the preferred skill set for most manufacturers. Utilizing lean practices helps offset the workforce challenge along with increasing productivity and keeping waste at a minimum. The overall demand for someone with a lean background exceeds one with Six Sigma experience by a sizeable 129%.
In the study, job postings that specifically require Six Sigma are down to 13%. That’s significantly down from 27% in the 2013 study. In the 2013 study, 43% of lean jobs also required a Six Sigma skillset. The trend appears to be in favor of lean manufacturing principles.
What is Lean Manufacturing?
For those unfamiliar with lean manufacturing processes, it is a way for manufacturing companies to improve efficiency and effectiveness by eliminating waste. Whereas Six Sigma identifies and removes the causes of defects and minimizes variability in manufacturing processes. The lean process was first introduced in the earlier part of the 20th century to address many challenges the industry faced. It was later rebranded in the late 1980s as “lean” by a reporter who published an article about the benefits of implementing lean. One reason lean principles are currently popular with manufacturers is it increases productivity to optimize efficiency. It is now the preferred manufacturing method for many companies domestically and globally.
There are a variety of reasons that are making manufacturing companies rethink their production process and look at how they can be more profitable while competing on a global scale. One of the reasons includes companies looking to consolidate their limited resources around lean to address the challenges impacting current economic conditions. Lean’s practical approach to addressing waste, production flow, and flexibility aligns with modern manufacturers’ immediate needs.
Lean manufacturing processes, in comparison to Six Sigma’s, is an alternative method that focuses more on eliminating waste while improving efficiency. Companies also feel their lean operations need more development. So, they hire staff with this skillset or experience to ensure lean is optimized at their facilities. APG believes more companies have underestimated what it takes from a time and talent resource perspective to go from a tools-based approach to a process that lean is completely implemented into their operations.
In addition, many manufacturers continue to direct their attention to continuous improvement efforts on leaning their operations by eliminating waste, putting standard work in place and developing their throughput, which they focus later on reducing process variation and utilizing a Six Sigma approach. Some companies will have a well-integrated approach, but the majority will tend to navigate towards lean principles.
Why Six Sigma Still Matters
Although both Lean and Six Sigma principles end up with similar results and tend to overlap, lean maximizes productivity for a workforce. Having both skillsets is necessary for employers so they have a well-rounded workforce that can produce products in the most efficient, productive, and effective manner.
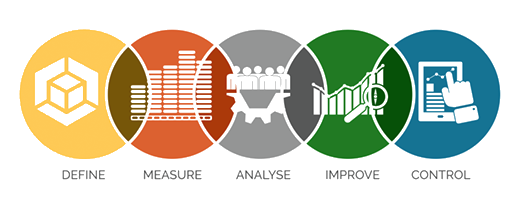
Taking advantage of Lean and Six Sigma courses offered by their local MEPs to ensure their staff receives enough hands-on training to grow their business is a must. Many newer employees and candidates don’t have the experience to fulfill their roles. According to the APG study, the shift to lean practices has contributed to the lack of recent on-the-job skills for many candidates. Sometimes it’s caused by poor training and certification. Courses taught at MEPs throughout the nation are carried out by industry experts with decades of experience to ensure individuals receive the proper training.
APG stressed the importance Six Sigma has on Continuous Improvement work to solve complex systemic process challenges through targeting process variation, process yield and to gain a better understanding of the input factors that spur a process’ overall performance and capability. “The overall foundation of Continuous Improvement should be viewed as a collection of complementary tools that integrates both Lean and Six Sigma, which are then applied as appropriate.”
Both Lean and Six Sigma principles can and should be applied; however, current industry disruptions have caused companies to favor Lean which can deliver a more immediate ROI when the focus is placed on waste, flow, and flexibility. For employers investing in their talent, they can grow and nurture their employees in their roles. This will address the ever-present challenge of finding new, qualified workers. Instead of constantly looking for that perfect candidate, employers will develop their own, skilled, loyal team. With the demand for both Lean and Six Sigma principles, there are Lean Six Sigma training courses that combine both methods. Taking advantage of practical Lean and Six Sigma training will give domestic manufacturers the edge they will need to compete in this increasingly competitive and challenging business landscape.