Distek Inc. Donates 3D Printer to Foster Training Opportunities
NJMEP Client Donates 3D Printer to Ensure the Machine Goes Where It Will Be Put to Use, Training the Next Generation of Creators and Makers
WHO IS DISTEK INC.?
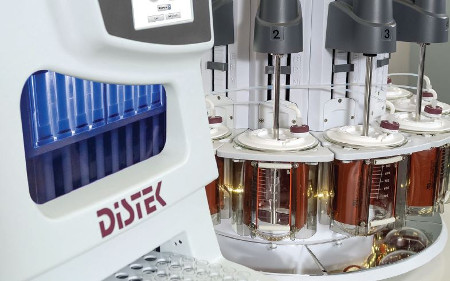
With over 47 years of experience, Distek is a North Brunswick, family-owned, manufacturer of laboratory testing equipment for the pharmaceutical and biotech industries, specializing in benchtop instruments that help companies streamline research and development and quality control. Their industry expertise extends beyond manufacturing, offering customers proficient validation and qualification services.
“We make products here, and as a mechanical engineer I like that part of the business,” says Jeff Brinker, 2nd Generation President of Distek Inc., when asked whether he had always envisioned joining the family business and taking over after his father, who was a chemical engineer by trade and the founder of Distek. Following his college graduation and upon entering the workforce, Jeff moved out west and worked for about five years before feeling the tug to return to New Jersey. “I always had it in the back of my mind that I was going to eventually come back,” says Brinker, citing slight parental pressure as being one of the causes for getting involved with the family business.
DECIDING WHAT TO DO WITH THEIR OLD TECH
Distek recently upgraded their 3D Printing capability with a machine that can produce larger-scale components and can do so more efficiently. When it was time to decide what to do with their current, 15-year-old 3D Printer, Jeff decided it should go to someone who would use it—and donating it to a high school STEM program was the first idea.
“We contacted a couple local high schools to donate [the 3D printer] but didn’t get any response back, and I’ve had a couple meetings with [NJMEP] to talk about some manufacturing initiatives and improvements and things,” says Brinker, “And we were just walking through our office, and I asked if [NJMEP] knew anyone that could use the printer since we’re not really using it anymore.”
Dan Deutsch, NJMEP’s Engineering Manager and Subject Matter Expert for Engineering and Automation, who was on-site to perform a Business Assessment, suggested that NJMEP could find a use for it in our training programs or through the Pro-Action Education Network—an initiative that works with Community Partners, CTE schools, Vocational/Technical Schools, Community Colleges, and over 25 Career Centers, to create alternative pathways for students interested in STEM and Advanced Manufacturing careers.
“I asked him if he knew of anyone who would want a donation [of the 3D Printer] and he said, ‘You know what, we do training at our center and would love to have a printer,'” says Brinker. “And that’s it—it happened very quickly, and we were happy to be able to donate and give it away to someone who is going to use it.”
USING 3D TECHNOLOGY TO DEVELOP PRODUCTS

According to Brinker, the 3D Printer that was donated is about 15 years old and no longer suited the company’s needs. “As an engineer developing products [the 3D Printer] is a pretty fascinating technology,” he says enthusiastically. “It’s a phenomenal tool, and what used to take days and weeks to prototype a part,” explains Brinker, “You essentially can design something one day, print it—some parts can be done in a half hour, some have to run overnight, and you can have another part waiting for you the next morning when you come in. See how it works out, iterate, change it a little bit, and run another one. It’s really an amazing tool for engineers.”
The process prior to utilizing 3D Printing Technology used to take weeks as Distek’s engineers in the product development department would have to go through far more steps and procedures when developing new products. “Before 3D Printing, our engineers would have to take a 3D file, create a 2D drawing of it, send it to a machine shop, sheet metal shop, or some outside company to actually fabricate the part, which could take days, if not weeks to make,” says Jeff. “When we look at our product development process, one of the biggest bottlenecks is prototyping parts,” he explains, “Especially if you have parts that need tooling. If we have an injection-molded cover or housing or some type of metal casting, even to prototype those things they can take a couple months. Which now you don’t even need to make tools in the prototyping stage, you can just 3D print them and see if they work.”
The biggest benefit of utilizing 3D technology in the development stage is saving time on product research and development. The process takes a less theoretical and artistic approach and is replaced with a more practical method which employs equal parts of trial and error and physical testing—essentially, making the thing and seeing if it fits or works.
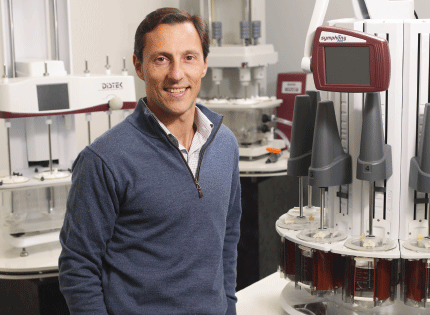
“For engineers during the development process to be able to design a part on their CAD package and just press the print button, send it over to the printer and get a part that same day or next day is pretty amazing,” says Brinker, “It just helps us be able to prototype and iterate so much faster.”
Jeff Brinker, President, Distek Inc.
Saving time is a critical element in the product development stage, especially since, as Jeff later goes on to say, time is money for manufacturers.
THE FUTURE OF 3D PRINTING IN MANUFACTURING
Jeff says that the future of engineering is going to be in tandem with advances in 3D Printing technologies. “I imagine 3D printing is going to play a pretty substantial role in the future of manufacturing,” he says. According to him, the next frontier for 3D printing is metal printing, which he says has been around for quite some time but is still in its early stages. As for what’s next for Distek Inc., it’s a little more prosaic. “We’re a New Jersey-based company, we manufacture in New Jersey— it’s where we’ve always been located, and all our products are designed and assembled in New Jersey. We’re proud to be a New Jersey company and we’re happy to be able to donate something to NJMEP that we know will get put to good use,” says Brinker.