A Leading Innovator in Advanced Manufacturing
Under the Leadership of MAC President Eddie Russnow, The Company Continues the Example Set by Founder Ed Gollob, Adopting Industry 4.0 Technologies Ahead of Their Peers
WE DON’T DO EASY

MAC Products Inc. began in 1968 with Founder and CEO Ed Gollob and just two other employees. Since those humble beginnings, the company has grown to over 100 employees, occupying a 4.5-acre fully integrated complex in South Kearny. MAC Products is a family-owned and operated manufacturer, with their leadership team now spanning three generations. MAC offers full-service, solutions-based, made-to-order manufacturing services and products, with clients ranging from electrical utilities to mass-transit entities. The company’s motto is that ‘We Don’t Do Easy,’ instead, they do business in a personal and honest way, and it’s the way they’ve done business for over 50 years.
As a longtime manufacturer deeply rooted in New Jersey, MAC has seen the onset of technological advancement within manufacturing time and again and has usually been at the forefront of innovation. What started as pencil and paper drawings has now evolved into one of the most technological operations in New Jersey Manufacturing. Eddie Russnow, President of MAC Products, offers a real masterclass in advanced manufacturing technologies—his background, not what you’d expect.
“Everything I did I learned on the job,” says Eddie, standing in his office in Kearny, the MAC Products Motto ‘We Don’t Do Easy’ emblazoned on the wall behind. “I was an international finance major in college, and I have a bachelor’s degree in international finance and thought I’d be working on Wall Street for my career,” says Russnow matter-of-factly, “Didn’t think I’d be in manufacturing. When I got the offer to come here, I looked at it and said, ‘Okay it’s probably a better opportunity for me.’ Then, I just embraced it and learned everything on the job, and I don’t have any regrets,” he adds. “I’m very happy and very passionate about the company and the work I do, and I love solving problems for people,” he continues enthusiastically. “That’s one of the things we do at MAC—We don’t do easy,” he says, pointing to the sign just over his left shoulder, “And the reason for that is that people don’t come to us when things are easy to do, they come to us when they have a problem—and we want to solve that problem for them.”
WHAT MOTIVATES MAC TO ADOPT NEW TECHNOLOGIES
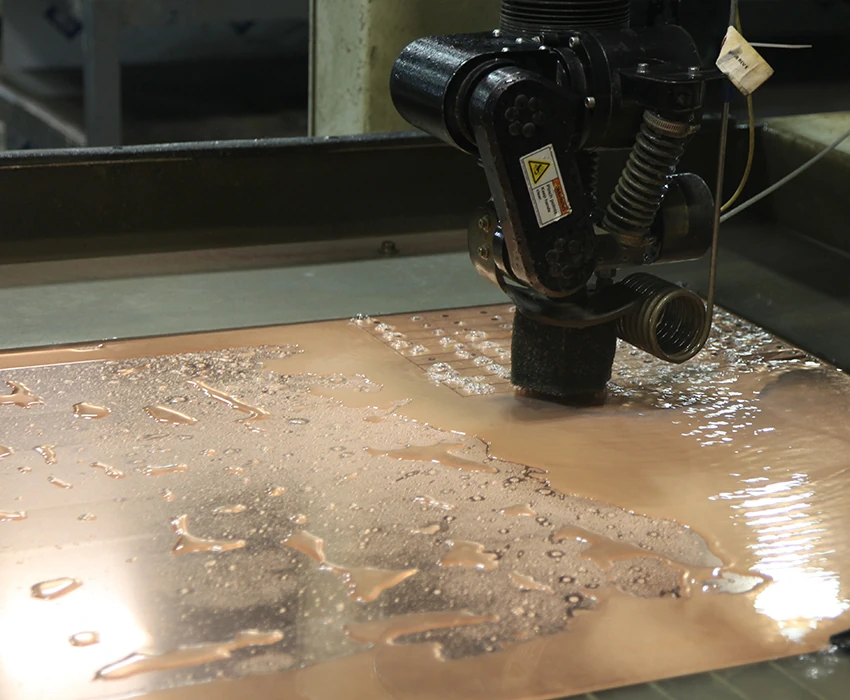
“When we started,” says Russnow, “The company was just using a lot of manual equipment, some of which we still have today because they’re still very useful in the production of low-volume items. We’ve been able to add capability onto it and to extend the life of that old equipment.” Solving high-level problems in a fast-paced and demanding industry like manufacturing in New Jersey calls for outside-the-box thinking and a lot of innovation. Sometimes this means taking leaps of faith and pursuing technological advancements that are untested—something MAC has been doing since the early days of advanced manufacturing. The company’s motivation?—their customers.
“The marketplace is dictating better service, and part of better service is being able to deliver quicker when the customer needs it and deliver where they want it,” says Russnow. “That’s been a push for us [with adopting advanced manufacturing technologies], to be able to service the customer base better,” he adds. “From an advanced manufacturing standpoint,” Eddie continues, “I remember when I first started here back in 1990, we had just started purchasing and utilizing CNCs. Over time, with the technology and capability evolving, we’ve moved to having four or five AXIS Machines, which has allowed us to produce more, to produce more challenging products, meeting critical and tighter tolerances.” Naturally, the evolution of technology has also been impacted by the need to keep up with demand, particularly in New Jersey where we have a dwindling workforce.
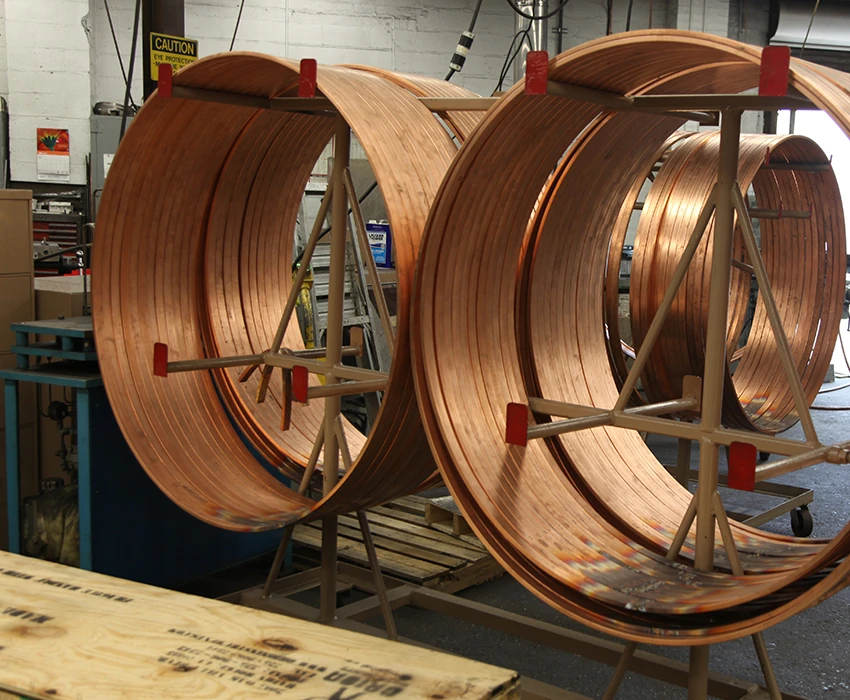
Eddie continues, “We are also adding on robotics to pieces of equipment so that we can have an operator working on three machines at one time, because we’ve added on a robotic arm. We’re not adding on full robotics, but we’re adding on a cobot, so that this operator can add more value to the business and more value to himself, by picking up this skillset.” Upskilling and reskilling their existing workforce is part of the MAC Products’ ethos. “[Retooling our workers] also allows them the opportunity to advance within the organization,” he adds, “We want to move away from having a person stand at a machine just to load and unload—that’s really no value add for the person there. By having the cobot, having the CNC and an automatic loader, we can run the business lights out.”
THE FUTURE OF MANUFACTURING WOULD BE DIGITAL
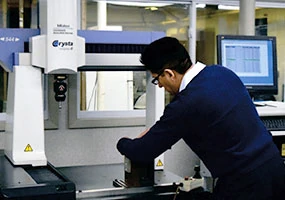
When businesses think about Industry 4.0, the first things that come to mind are automation technologies, robotics, cobots, and similar tech, but oftentimes one of the key components of this new industrial revolution is forgotten—software. After all, what good is automation technology if you don’t have the programming or technical know-how to operate these new advanced technologies? For MAC, this forwardthinking has been there since the early days of technology.
“When I started here, we were still doing pencil and paper drawings for CAD,” says Eddie, “And then, in order to get our team to buy into the computer software, my fatherin- law [Ed Gollob, Founder of MAC] actually purchased the first suite of software for us and sat in his office with the door closed for two or three weeks to learn it himself. He then brought in all of our engineers to demonstrate to them how easy it was. So he took it upon himself to show them that this is where manufacturing was headed—the future of manufacturing would be digital.”
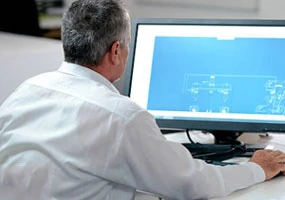
Russnow continues: “That’s how we started down the road of that engineering technology, and now of course, anybody that comes in—new staff, recent college graduates—the benefit to that is that they’re so advanced with the new technologies that they show the old guard new tips and tricks. That’s a huge benefit we’ve seen, even with interns that we’ve had who are really advanced in CAD and 3D modeling and design.”
MAC Products has been able to continually adapt to new technologies since its start over fifty years ago, and one of the key elements has been opening itself up to these new technologies, new methods of thought, and collaborating with younger generations of engineers and manufacturing professionals.
CONTENDING WITH A BROADENING SKILLS GAP
“The struggle in New Jersey is finding qualified people, and finding people that have the proper work ethic,” says Russnow. “That’s been a big change and certainly something that I hear from other manufacturers—there’s not the work ethic that most of us grew up with and are accustomed to seeing and expecting.”
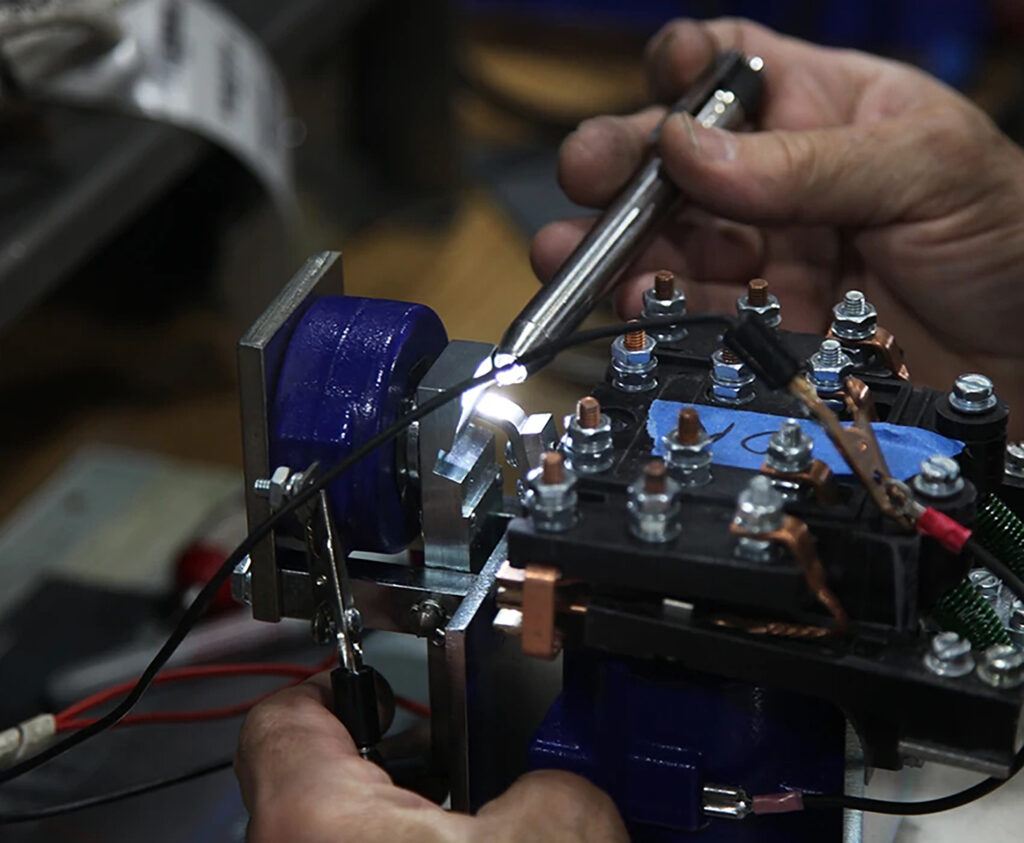
How does an organization contend with this shifting paradigm in work ethic and expanding skills gap? By getting more of buy-in from your organization’s greatest asset—its employees.
“A lot of it is communicating with your staff to explain to them what it is that you do—what’s your ‘why’ and ‘why do you do what you do?’” says Russnow. “I think that’s a very important piece of getting people to buy-in and understand why it’s so important to come to work on-time and why it’s important to be here every day, and it’s because we have customers that rely on us and the work that we do at MAC is critical to the infrastructure to this country—the electrical and mass-transit infrastructure. So, we try to explain to our staff, this is what we do. You’re just not here every day to drill a hole and tap a hole in a product. This is what you’re doing, this is where it goes, this is what the end part looks like, and this is why it’s important. If you explain that to them and take the time to do that, you can get them to have pride and ownership in the work that they’re doing and to have a strong work ethic,” he adds.
This is another area where MAC deploys Industry 4.0 technologies to help foster a better work ethic and also to give their employees more ownership of their roles. “On the shop floor we have a variety of different technology that we’ve been utilizing to monitor the effectiveness of our CNC equipment,” says Eddie. “Which has been a huge benefit to us because it opens your eyes to see how well we’re doing,” he adds, “And the staff has really bought into it because they want to know that they’re doing a good job.”
TAKING ADVANTAGE OF YOUR RESOURCES
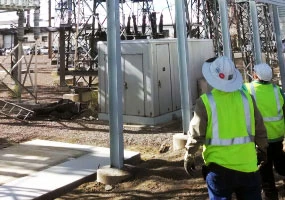
Another key area of concern for manufacturers in New Jersey is supply chain stability and reliability. Something that programs like CONNEX New Jersey—a new supply chain management tool—and the New Jersey Manufacturing Voucher Program are helping to support.
“If we’re having problems with the supply chain, the things that we can control within our facility is to manufacture as much as we can here,” says Eddie. “When we might have a problem with a supplier, with the use of technology and other things, let’s bring it back here and not outsource. We are a manufacturer, we have those capabilities, let’s look to advance our capabilities so that we don’t have to rely on others to control the destiny of our products,” he adds.
That’s where the NJMVP Program comes in to give MAC the support needed to expand their capabilities and extend their technological capacities. “We received a grant [as part of the NJMVP] for a piece of equipment that we’re currently waiting for,” says Russnow. “We bought a CNC Iron Worker to improve the throughput of a lot of our fabrication for certain products and projects that we do work on now, but that will allow us to increase the capacity in that area of our shop, and therefore be able to deliver faster and be able to take on more of that work,” he adds.
Sometimes, navigating programs like the NJMVP can be difficult for businesses who may not understand the process or have the time to dedicate to researching, educating themselves, and applying for government assistance—something Eddie and the MAC team can speak to. “The program had some little hiccups but nothing major,” says Eddie. “A lot of it was maybe we didn’t understand certain things about how to upload certain information, but at the end of the day it worked out well. Hopefully, the state will continue to offer this program and keep it in the budget,” he adds enthusiastically.
EVERY PROJECT IS A CLEAN SLATE
MAC has entrusted NJMEP for nearly a decade with consulting and training services—working together on Workforce Development, Marketing, LEAN, and Management training. Fruitful partnerships like this help New Jersey manufacture success, especially for an organization like MAC who as Eddie puts it in his own words:
“Every project we’re starting from scratch—a clean slate, like an artist.”
Eddie Russnow, President, MAC Products Inc.
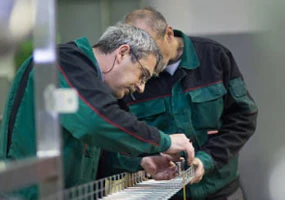
Only by taking advantage of your resources and leaning on manufacturing partners can the industry weather the distinct challenges it faces. Regardless of how secure you feel about your operation, there’s always room to improve, and always areas that can benefit from a third-party perspective—especially when it comes to process improvement or LEAN Manufacturing.
“We’re going through a process improvement project right now on a grant that we received through the State with the help of NJMEP,” says Russnow. “[With the help of NJMEP], we recognize that a lot of the issues that we’ve had in recent years are the fault of the process and some of the processes that we don’t have in place, or that we don’t follow consistently,” he continues, “[NJMEP has] been essential for us in a lot of the advancements that we’ve been making.”